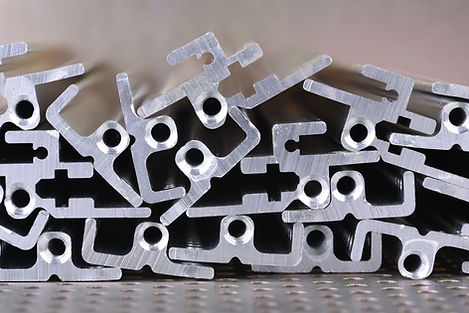
It's time to recycle...
ALUMINUM DEOXIDANT INGOT
Our aluminum deoxidants are versatile and high quality products specifically designed for use in the steel industries. These deoxidants are made from premium aluminum and are used in numerous applications in the steelmaking processes. They are used to remove oxygen content during steel production. Deoxidation is important in the steelmaking procedure as oxygen is often contrary to the nature of the steel formed. Deoxidization is most often accomplished by adding a different substance to counteract the effects of oxygen or by directly evacuating the oxygen. They are also used as a source of alloying elements such as aluminum in steel production. By adding aluminum deoxidants to molten steel, alloying elements are added, resulting in better strength, corrosion resistance, and other desired properties. Our aluminum deoxidants are a reliable choice for improving the quality and performance of steel products in the steel industry.
Specifications: 95% min , 96% min , 97% min , 98% min
Deoxidation is the final stage in steel production. In Basic Oxygen Furnace (BOF) and other similar steelmaking applications, the steel bath has a drawing time of 400 to 800 ppm oxygen activity.Ibecause it contains. Deoxidation is carried out during draining by adding appropriate amounts of Ferro-Manganese, Ferro-Silicon and/or aluminum or other special deoxidants to the tap pot. If the carbon content of the steel is below specifications at the end of blowing, the metal is also recarburized in the crucible. However, large additions to the crucible are undesirable due to their adverse effect on the temperature of the metal.
Clean steel production is one of the constant concerns of alloy steel manufacturers. Deoxidation processes with different elements lead to the production of impurities, each of which causes a decrease in the mechanical properties of steel. Meanwhile, steels that require deoxidation with Aluminum or are present in this element analysis are more exposed to mechanical damage due to the presence of Aluminum impurities. Therefore, the amount as well as the process by which aluminum is added to the melt will have a significant impact on the quality of the steel.
Aluminum is mostly used in steel for deoxidation and denitrification. Therefore, it can have a good effect on susceptibility to aging phenomenon. Aluminum is often used as an alloying element in nitrided steels because it produces high-hardness nitrides with nitrogen. This element prevents the growth of grains by forming dispersed oxide and nitride compounds and thus helps the formation of fine crystal grains.
Aluminum narrows the austenite range very much. Aluminum is also used as an alloying element in Iron-Nickel-Cobalt-Aluminum permanent magnet alloys due to the large increase in strength with the magnetic field required for demagnetization.
In fact, the purpose of deoxidation is to reduce dissolved oxygen in steel to prevent the formation of impurity elements, remove gas voids, desulfurize and even control the grain size of steel. This process is called the melt, sedimentary deoxidation or mixing and reaction of steel, from iron (Calcium, Magnesium, Aluminum, Silicon, Manganese, Carbon, etc.). It contains oxygen with additional charges of high FeO capacity, called permeation deoxidation. In steelmaking, aluminum is an alloying element and also a powerful deoxidizer.
Aluminum is also used as an alloying element to increase the toughness of steel by controlling the grain size of the final product. To achieve both goals, the optimal amount of Aluminum must be defined.
The production of the aluminum hemispheres mentioned above is made with a previous order, and these dioxidants have been used in many steel factories in Turkey to date.